Het afgelopen jaar werden er 1,555 miljard smartphones verkocht. Data News ging op bezoek bij Huawei en Motorola en mocht daarbij de productielijnen van de P20 en de G7 bezoeken.
Motorola bezoeken we in het Braziliaanse São Paulo, waar het bedrijf voor de Latijns-Amerikaanse markt produceert. Huawei bezoeken we in hun thuisstad Shenzhen. Hoewel het twee verschillende bedrijven in twee uithoeken van de wereld liggen, vallen ons twee dingen op: beide productieprocessen lijken bijzonder hard op elkaar en er zijn relatief weinig menselijke tussenkomsten. Al hebben we de indruk dat er bij Motorola nog net iets meer (fijne) handenarbeid aan te pas komt.
Binnenwandelen doet u niet zomaar. Laptops en smartphones laten we achter aan de ingang. We krijgen een antistatische jas en voetbeschermers aan en volgen netjes de gids langs één van de productielijnen. Hoe moeten we ons dat voorstellen? Eén lange rij machines van zo’n 120 meter. Zo tellen we er bij Huawei een vijftal per verdieping. Elke rij produceert zo’n 2.400 toestellen per dag, een trip die zo’n 24 tot 48 uur duurt en begint bij een printplaat. Bij Motorola rolden er zo al meer dan 220 miljoen stuks van de band sinds die in 1996 werd opgestart.
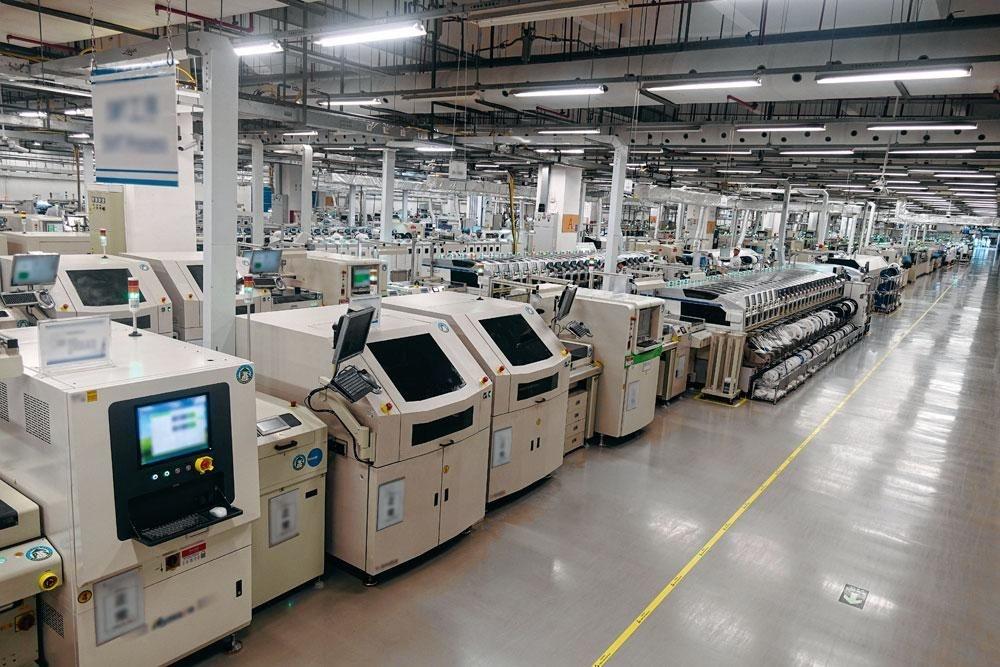
De eerste stap voor zo’n plaat is een stevige insmering met soldeerpasta. Zo kunnen vervolgens de componenten machinaal op het toestel worden gezet. Die onderdelen, zoals de processor, worden aangeleverd op spoelen die nog het meest doen denken aan oude geluidsrecorders. Op zo’n band zitten honderden identieke componenten die op het toestel worden gezet met een precisie van minder dan 0,4 millimeter. De optische inspectie tussendoor haalt er regelmatig foutjes uit en stuurt zo’n ‘panel’ terug naar het begin van de rij. De ‘error rate’ is in deze fase van het productieproces het hoogste, horen we bij Motorola, net omdat dit het meest precieze werk van de hele assemblage is.
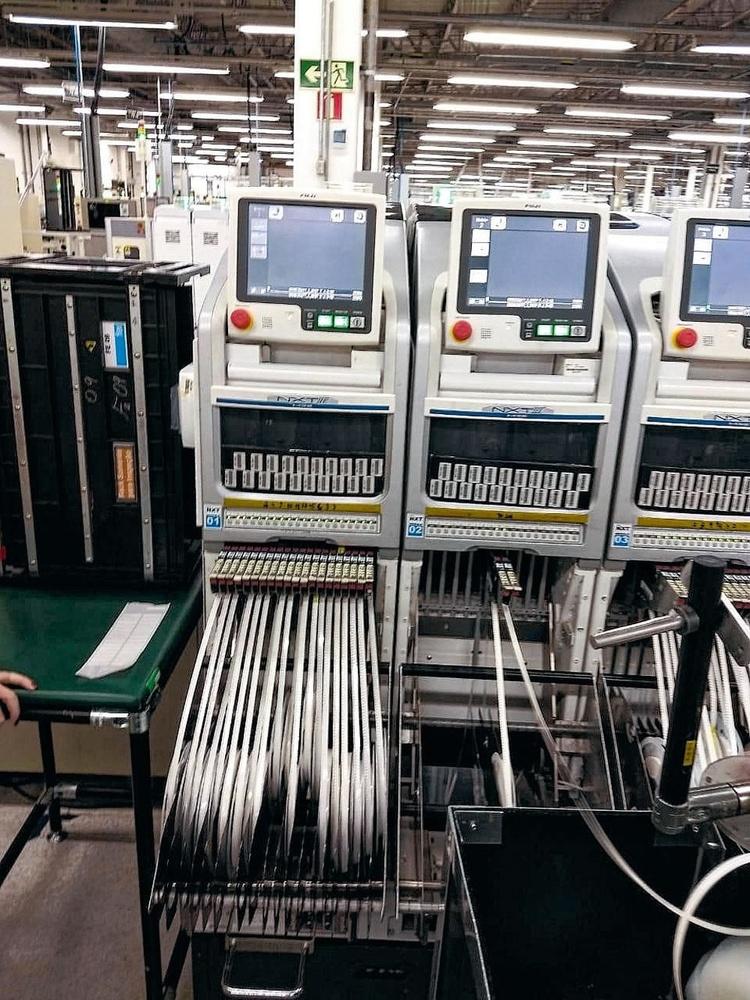
Wat dan weer niet machinaal gebeurt bij Huawei, is de cameramodule. De smartphones komen even uit de machine, waar een arbeider ze voorziet van een blokje met onder meer de cameralenzen erin. Al wordt het blokje wel door een machine aangeschroefd.
Op één productielijn van Huawei werken gemiddeld maar zeventien mensen, vijf jaar geleden waren dat er nog meer dan tachtig
Op één productielijn van Huawei werken gemiddeld maar zeventien mensen. Het bedrijf streeft naar zo veel mogelijk automatisering. Een goede vijf jaar geleden waren dat er nog meer dan tachtig per lijn. “Wij zetten nog volop in op verdere automatisering”, vertelt Paulo Caixeta, product engineer bij Motorola Mobility. De fabriekssite stelt momenteel nog 5.500 mensen te werk – al horen daar ook R&D, prototyping, distributie, en service & herstelling bij.
Dat de machines overheersen in de assemblage, merken we overigens ook in het distributiecentrum van Huawei. Voor de volledige productiesite, waar ook routers en andere hardware wordt gemaakt, zijn er maar 145 mensen nodig. Componenten worden machinaal uit metershoge rekken gehaald en op de werkvloer aangeleverd met kleine transport-robots. Afgeleverde producten gaan via diezelfde robots of per transportband naar de juiste bestemming.
Hoewel er op het eerste zicht veel gelijkenissen zijn tussen het productieproces bij Motorola en Huawei, laat Huawei wel verstaan dat een groot deel van haar machines zelf zijn ontworpen. Dat maakt het bedrijf naar eigen zeggen beter in de assemblage. Motorola legt er dan weer de nadruk op dat het voor veel automatisering ook beroep doet op Braziliaanse (robotica)bedrijven.
Testing
In theorie kan een smartphone op 24 uur tijd doorheen het assemblageproces gaan. In praktijk duurt dat soms dubbel zo lang. Dat komt omdat er tussen de verschillende fases regelmatig een test wordt uitgevoerd. Zo wordt, nog voor de behuizing rond de telefoon wordt gezet, de telefoon door een robot van de band genomen en in een schuifje gezet. Daar wordt onder meer getest of de telefoon ook bij hogere temperaturen in goede staat blijft, maar ook of er problemen kunnen zijn met de frequenties die het toestel uitzendt.
Na die testing komen de toestellen automatisch weer op de productieband. Daarbij merken we op dat er ook een aantal QR-codes zijn bijgekomen. Die zijn er vooral voor de kwaliteitscontrole. Mocht er achteraf toch iets met het toestel schelen, dan kan Huawei vrij exact zeggen om welke batch toestellen en componenten het gaat, waardoor een probleem veel beter kan worden geïsoleerd van de rest van de productie.
Nu de interne hardware is getest, wordt het scherm toegevoegd. Dat gebeurt door het twee uur lang op het toestel te drukken. Zelfs nadien blijft het toestel zo’n tien uur in rust liggen voor extra stabiliteit. Nog de behuizing en batterij, en de telefoon is de facto klaar.
Vervolgens is het de beurt aan een zogenaamde ‘burning test’. De telefoon wordt bij een temperatuur van dertig graden opnieuw getest, deze keer niet enkel op frequenties maar op alle componenten. Zo wordt het toestel aangezet en worden zowel hard- als software belast.
Gaat het vaak fout in zo’n proces? Relatief weinig. Huawei zegt dat het aantal foute componenten in het assemblageproces slechts 2,87 per één miljoen is. Dat is wel enkel voor het assemblageproces, dus zonder de productie van de processor, batterij of andere onderdelen. Huawei maakt (net zoals Apple en Samsung) haar processor zelf. Motorola doet doorgaans een beroep op chips van Qualcomm.
Het geluid, de batterij en de camera worden apart getest. Opmerkelijk: in tegenstelling tot de overige twee wordt het geluid bij Huawei grotendeels handmatig getest. De telefoons komen in een kleine (bijna) geluidsdichte ruimte waar een werknemer nagaat of het geluid naar behoren is. Meteen de enige plaats op de productielijn waar een arbeider kan zitten.
Voor het ‘fijne’ werk doet Motorola letterlijk beroep op fijnere handen: zowat iedereen aan die productielijnen is vrouwelijk.
Opmerkelijk bij Motorola trouwens: voor het ‘fijne’ werk doet het bedrijf letterlijk beroep op fijnere handen. Zowat iedereen aan die productielijnen is vrouwelijk. Geen toeval, zegt Motorola ons: “De handen van de meeste mannen zijn nu eenmaal te groot om dit precieze werk te kunnen uitvoeren.”
Doorstaat het toestel het examen, dan is het tijd voor het verpakkingsproces. De telefoon komt in een doos, aangevuld met handleidingen, oplader en eventuele accessoires. De laatste stap in het proces is de weegschaal. Zo weet de fabrikant of het toestel mogelijk onderdelen ontbreekt (of te veel heeft). Bij Huawei mag een smartphone zes gram van het ideaalgewicht afwijken, bij Motorola is dat amper een gram: “Voldoende om zelfs te detecteren dat het verplichte compliancy-papiertje niet in de doos zit”, verzekert men ons.
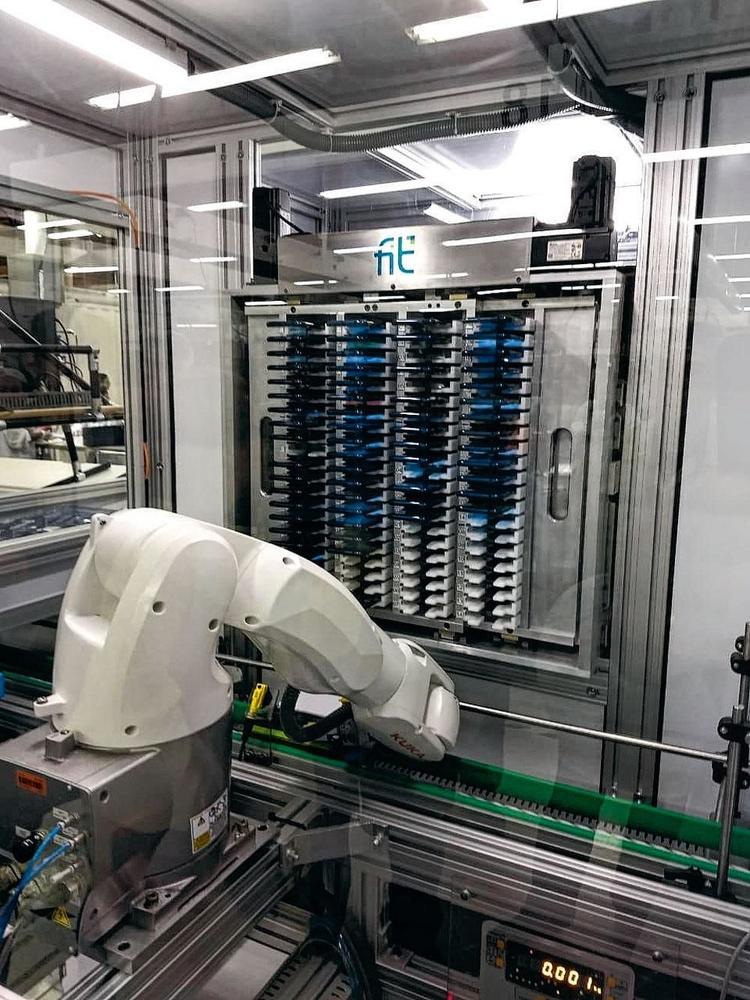
Hoe test u een zendmast?
Huawei maakt naast smartphones onder meer ook zendmasten en die moeten getest worden. Daarvoor bezoeken we hun Spherical Near Field Test System, een afgesloten ruimte van 10x12x15 meter waar een base station kan worden getest. Huawei test elk nieuw base station dat het op de markt brengt en 1 procent van alle commerciële base stations die het verscheept.
Op de foto hieronder ziet u het base station in het midden. De oranje ring meet de signalen rondom de antenne. Die antenne kan trouwens draaien, waardoor de ring het signaal in 350 graden kan meten. De vele pieken die u rondom de ruimte ziet, moeten de signalen weer neutraliseren. De kamer is zodanig gebouwd dat er binnenin geen enkel signaal van buitenaf meetbaar is, en omgekeerd dat de zendmast die wordt getest geen invloed heeft op activiteiten in de rest van het gebouw. Huawei heeft één kamer van dit kaliber en nog twee kleinere gelijkaardige ruimtes waar andere draadloze apparatuur wordt getest. De kamer zelf wordt geleverd door het Franse SATIMO.
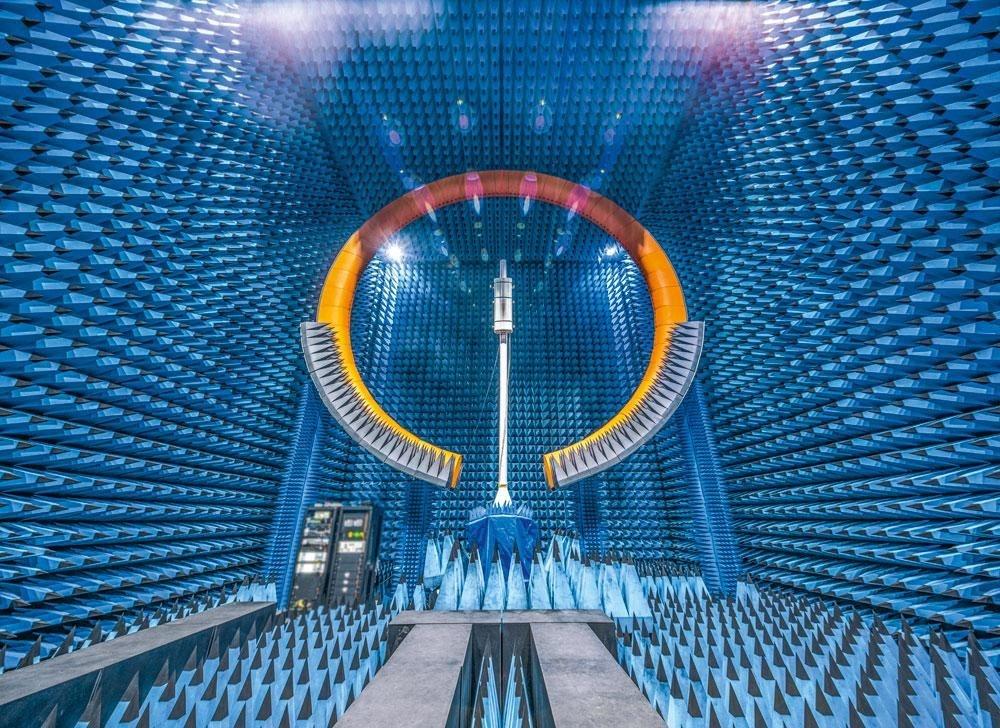