De nieuwe bril van Odette Lunettes, het brillenmerk van Vlaamse tv-persoonlijkheid Eline De Munck, wordt op de markt worden gezet als duurzaam, omdat hij via 3D-printing en uit natuurlijke materialen is gemaakt. Maar hoe duurzaam is duurzaam?
De brillen, gepromoot door ex-wielrenner Tom Boonen, worden geleverd door het Leuvense techbedrijf Materialise. Het raakte ooit bekend in volle ‘print uw eigen 3D-bestanden’-hype, maar werkt ondertussen aan alles van prototypes voor de auto-industrie, over medische hulpmiddelen en op maat gemaakte inlegzolen, tot dus ook brillen. In dit geval print Materialise de monturen, vaak op maat. De glazen en schroefjes worden er achteraf in gemonteerd.
Kleinere oplages
‘Eye wear is een van de applicaties die zich uitermate leent voor 3D’, zegt Jurgen Laudus, vp en general manager Manufacturing bij Materialise. ‘Je kan kleinere oplages printen, en ontwerpen gebruiken die met klassieke mallen misschien niet lukken. Het proces is ook duurzamer, omdat je bijvoorbeeld geen montuur uit een groter blok gaat snijden.’
De meeste brillen worden echter niet gefreesd, maar gemaakt met een mal waarin bijvoorbeeld het plastic wordt gegoten. ‘Dat gebeurt ook vaak aan de andere kant van de wereld om de kosten te drukken, en daar zit je met een stockrisico’, zegt Laudus. Om de kost van het maken van zo’n mal terug te verdienen, moet je met andere woorden heel veel brillen verkopen. En als dat niet lukt gaan die op de afvalberg. De oplossing die Materialise voorstelt om duurzamer te werken is dan ook simpel: minder produceren en lokaal produceren. ‘Bij ons kan je echt kleine reeksen maken, van duizend of tweeduizend stuks. Als de vraag groter is, print je gewoon exemplaren bij.’
Voor kleinere oplages zou deze productiewijze zelfs voordeliger zijn, net omdat je spaart op transport en overschotten. ‘En de ultieme vorm van zo’n kleine reeks is dan nog een gepersonaliseerde bril, op maat gemaakt van het gezicht van de klant’, aldus nog Laudus. Het bedrijf experimenteert ondertussen met scansystemen bij opticiens die de afmetingen van je gezicht, oren en neus optekenen om je tien dagen later een gepersonaliseerd exemplaar te leveren, vers van de 3D-pers.
Overschot
De nieuwe bril van Odette Lunettes maakt meteen ook gebruik van een nieuw soort materiaal, genaamd PA11. ‘Dat is een biogebaseerd nylon, gemaakt uit castorbonen’, aldus Laudus. De castorboom wordt in India geteeld op arme grond, en van de olie uit de bonen wordt plastic gemaakt. Een en ander moet de CO2-uitstoot bij het produceren van het nylon met de helft verminderen tegenover de meer traditionele plasticsoorten die voor dit type 3D-printing worden gebruikt.
Maar hoe zit dat dan met die overschot? Grote producties van 3D-printing gebruiken niet, zoals de kleine thuisprinter, een variatie op het inkjetsysteem dat de component laagje per laagje met gespoten plastic opbouwt. De technologie aan het werk hier is ‘laser synth’, ofte printen in een grote bak gevuld met poeder. ‘Dat poeder wordt aan elkaar gesmolten bij 180 graden. We warmen die bak op tot 170 graden en gaan vervolgens met een laserestraal energie toevoegen om het montuur op te bouwen’, klinkt de uitleg.
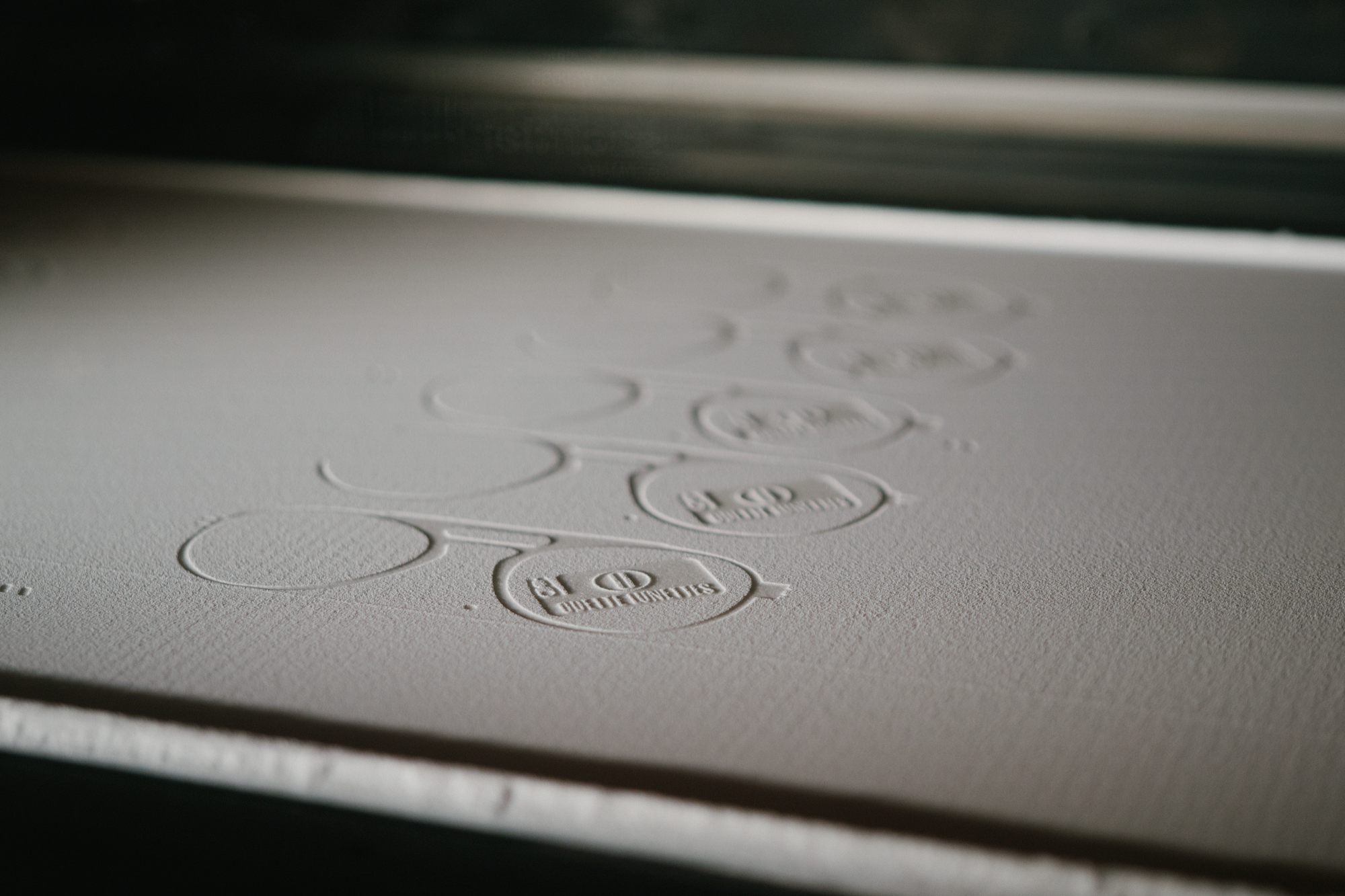
Laudus toont in de fabriekszaal hoe dat werkt. In de 3D-printer wordt op een grote plaat een dunne laag wit poeder gedeponeerd. Met een laser gaat de printer daarin de juiste elementen aan elkaar smelten. De plaat schuift vervolgens een fragment van een millimeter naar beneden, en er komt een nieuwe laag poeder over, waarin ook weer enkele elementen worden ‘gefuseerd’. Aan het einde van de rit heb je een bak met een hele reeks geprinte componenten, in dit geval brilmonturen. Dat ruwe product wordt uit de bak gevist, afgestoft en verder afgewerkt door het bijvoorbeeld glad te schuren en van een kleur te voorzien.
Stof voor recyclage
De methode bestaat al een tijd, en waar de componenten vroeger nog met tussenstukjes (of ‘supports’) aan elkaar hingen bij het opbouwen, is de technologie ondertussen geëvolueerd naar minder restafval, en meer efficiëntie. Er worden door verbeteringen in de software bijvoorbeeld steeds meer componenten Tetris-gewijs in zo’n bak gepropt, met minder ongebruikt poeder als resultaat.
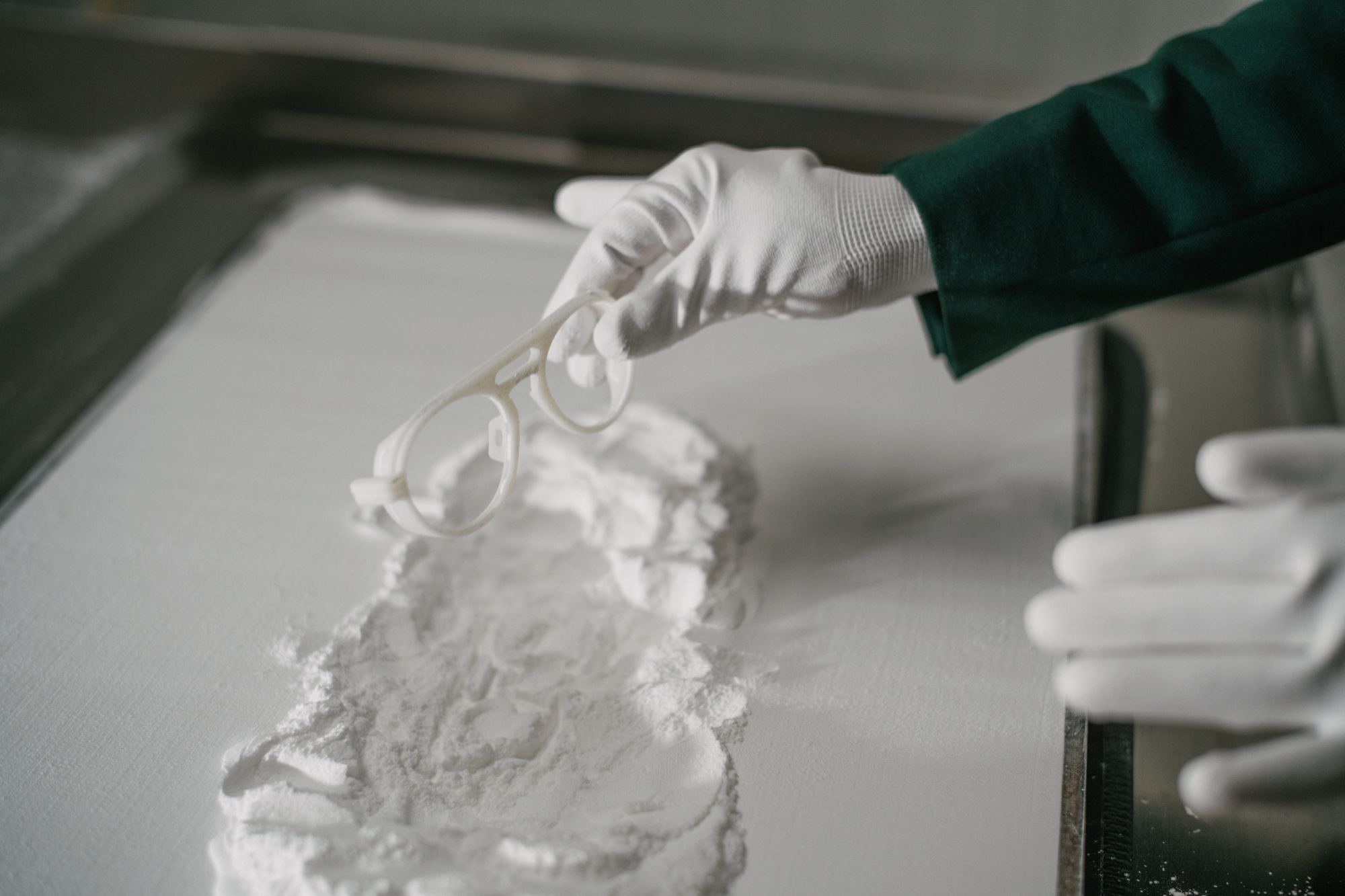
Ook het niet-gesmolten poeder wordt opnieuw ingezet, zegt Laudus. ‘Maar dat veroudert wel, dus je kan het niet eindeloos hergebruiken. Daarom hebben we bij Materialise de BlueSynth-technologie ontwikkeld waardoor we in bepaalde machines met oud poeder toch nog goede stukken kunnen maken.’
Software
Dat laatste gebeurde in samenwerking met de software-afdeling, want het bedrijf heeft zich de laatste jaren ook toegelegd op het ontwikkelen van besturingsprogramma’s voor 3D printers.
‘We zijn daar ooit mee begonnen om onze eigen printers beter aan te drijven, maar dat is nu een commercieel product’, zegt Laudus. Materialise levert tegenwoordig ook software aan andere bedrijven die een 3D-printer hebben. ‘Het gaat dan om het voorbereiden van de data om te gaan printen’, legt hij uit, ‘maar ook software om te machine aan te sturen, om de meest efficiënte baan te vinden die de lasterstraal moet schrijven, bijvoorbeeld. We komen altijd korter bij de machine.’ Het zijn kleine stapjes vooruit die het systeem altijd efficiënter, en duurzamer, moeten maken.